CiA® 436 series: CANopen application profile for construction machines
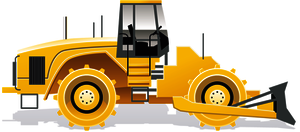
The profile specifies the use of CANopen networks on construction machinery by introducing a virtual control architecture. This architecture integrates the interfaces to the (diesel) engine control system, the driver's desk, the sensor control system, the transmission control system, the fleet management control system, and the implement (superstructure) control system. CiA 436-1 specifies the integration network with the interfaces to the mentioned subsystems. A separate application profile is specified for each subsystem.
The idea for an integration network came from the rail industry. Unfortunately, the construction industry does not use such integration networks, yet. Instead, the main controller is typically connected to all networks. The currently valid CiA 436-1 version 1.1.0 has been available since June 2010. The sub-network for sensor control systems is specified in CiA 415. Other parts of CiA 436, which specify additional sub-networks, are in development.
Interested parties are invited to participate in the development of further subsystems.
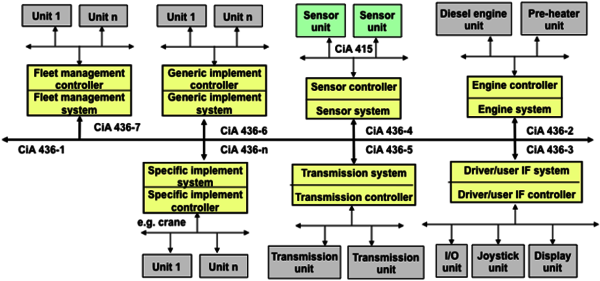
The general physical layer definitions for CANopen CC devices (see CiA 301) apply. Compliant devices support bit rates of 125 kbit/s, 250 kbit/s, and optionally higher. The 7-pin connector and the 5-pin micro-style (M12) connector with CiA 106 pinning are recommended for the CANopen network connection. An additionally defined application-specific 8-pin round connector does not comply with CiA 106. CANopen devices implementing this profile support the CANopen status and error LED (see CiA 303-3).
It is recommended that the CANopen NMT manager functionality resides on the device interfacing with the driver's desk control system. Other systems provide CANopen NMT server functionality. The node-ID assignment is manufacturer-specific. For node-ID assignment via CAN (e.g., for IP67-rated devices), the CANopen layer setting services (LSS, see CiA 305) may be used. The Heartbeat functionality is used for error control. In addition to the reaction to a communication error and an internal device error, the reaction to a sub-network failure is configurable. The object 1000h indicates the type of the CANopen device and its functionality, such as a generic construction machinery controller or the interface to a specific subsystem. This profile provides no PDO definitions, no special redundancy concepts, and no special mechanisms for safety-related data communication. If such functionalities are required, the definitions given in the corresponding documents (namely CiA 301, CiA 302-6, and EN 50325-5) apply. The general device parameters contain information about the used machine (type, manufacturer, serial number, etc.), fleet management, superstructure (type and serial number), date and time, as well as the operating hours.
Title | Details | Published Size |
Status Action |
---|---|---|---|
|
ScopeThis document recommends the connector pin-assignment for CAN interfaces. This includes the CAN_H and CAN_L pins, the ground pin, and the power supply pins. |
2023-07-11 896 KB | TR Login |
|
ScopeThis specification specifies the CANopen application layer. This includes the data types, encoding rules and object dictionary objects as well as the CANopen communication services and protocols. In addition, this specification specifies the CANopen network management services and protocols. This specification specifies the CANopen communication profile, e.g. the physical layer, the pre- defined communication object identifier connection set, and the content of the Emergency, Time- stamp, and Sync communication objects. |
2011-02-21 3 MB | PAS Login |
|
ScopeThe network redundancy is intended to be an add-on to the CANopen application layer and communication profile (see /CiA301/). It is assumed, that a CANopen device with the need of safety-critical and mission-critical communication can use all the features defined by the communication profile. Safety -critical and mission-critical communication is achieved by the underlying structure defined in this specification. The manufacturer and the system integrator shall take care, that the hardware and software of the CANopen device support the safety-critical and mission-critical function and that the CANopen device is operated within its safety-critical and mission-critical limits. |
2009-02-02 512 KB | DSP Login |
|
ScopeThis recommendation describes the communication-related indicators. Additional application- related indicators are either described in the appropriate device profile or are manufacturer-specific. |
2012-04-27 237 KB | TR Login |
|
ScopeThis document specifies the layer setting services (LSS) and protocols for CANopen. These services and protocols are used to inquire or to change the settings of three parameters of the physical layer, data link layer, and application layer on a CANopen device with LSS slave capability by a CANopen device with LSS master capability via the CAN network. The following parameters may be inquired or changed: • Node-ID of the CANopen device; • Bit timing parameters of the physical layer (bit rate); • LSS address compliant to the identity object (1018h) |
2013-05-08 2 MB | DSP Login |
|
ScopeThe CANopen sensor system application profile for road construction and earth moving machines specifies the communication interface for sensors as well as the sensor control unit. The profile is suitable for a broad range of machine types (e.g. paver, compactor, grader, dozer, mill, heater and truck). NOTE The first version of this profile has been jointly developed with the OSYRIS (Open System for Road Information Support) consortium (www.osyris.org) and the European Asphalt Pa vement Association (EAPA). |
2009-04-22 2 MB | DSP Login |
|
ScopeThis application profile provides general definition as well as recommendations for using CANopen control networks on construction machineries. In addition, this applicat ion profile introduces the virtual control architecture on construction machineries, integrating the engine control system, the drivers’ desk, the sensor control system, the transmission control system, the fleet management control system as well as the co ntrol system for the superstructure respectively implement. |
2010-06-30 530 KB | DSP Login |