CiA® 420 series: CANopen profiles for extruder downstream devices
Members of CiA and Euromap have collaborated to develop CANopen profiles for extruder downstream devices, such as pullers, corrugators, saws, calibration tables, and co-extruders. These devices operate with NMT (network management) server functionality only, while the extruder manager provides both NMT manager and server roles, handling all heartbeat and EMCY (emergency) messages from the downstream devices.
The CiA 420 profile set enables seamless integration of downstream devices from different manufacturers. Euromap adds further specifications for local non-CANopen interfaces, covering emergency-stop wiring, a discrete measuring wheel interface, and non-CAN interfaces for saws.
The CiA 420 series defines CAN bit rates, connectors, cabling, and node-IDs. According to CiA 420, downstream devices receive control commands via RPDO (receive process data object) and send status responses via TPDO (transmit process data object). The PDOs also contain process setpoints and actual values, meaning extruder manager commands are confirmed at the application level. It also specifies PDO communication and mapping parameters for various downstream devices. All PDOs support synchronous transmission and reception, with a SYNC cycle time of 20 ms. Configuration parameters are written and read using the default SDO (service data object) channel.
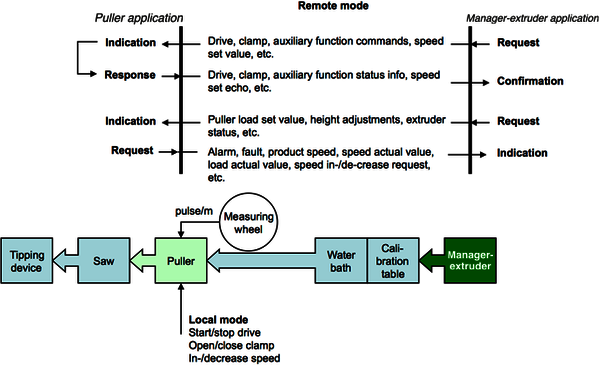
The set of profiles comprises the following parts:
- Part 1: General definitions (including connector and node-ID assignment)
- Part 2: Puller
- Part 3: Corrugator
- Part 4: Saw
- Part 5: Simple and advanced co-extruder
- Part 6: Calibration-table
Title | Details | Published Size |
Status Action |
---|---|---|---|
|
ScopeThe CANopen application profile for extruder downstream devices includes several parts: Part 1 specifies general definitions; Part 2 specifies the device profile for the puller downstream device; Part 3 specifies the device profile for the corrugator downstream device; Part 4 specifies the device profile for the saw downstream device; Part 5 specifies the device profile for the co-extruder device; Part 6 specifies the device profile for the calibration-table downstream device. NOTE All parts of this specification have been developed jointly with the European Committee of Machinery Manufacturers for the Plastics and Rubber Industries (Euromap) and is documented there as Euromap 27. This part specifies the physical layer and the common CANopen functions and common communication objects. It also specifies the CANopen functions of the extruder-master. |
2015-05-07 657 KB | PAS Login |
|
ScopeThe CANopen application profile for extruder downstream devices includes several parts: Part 1 specifies general definitions; Part 2 specifies the device profile for the puller downstream device; Part 3 specifies the device profile for the corrugator downstream device; Part 4 specifies the device profile for the saw downstream device; Part 5 specifies the device profile for the co-extruder device; Part 6 specifies the device profile for the calibration-table downstream device. NOTE All parts of this specification have been developed jointly with the European Committee of Machinery Manufacturers for the Plastics and Rubber Industries (Euromap) and is documented there as Euromap 27. This part specifies the CANopen interface for the puller downstream device. |
2015-05-07 475 KB | PAS Login |
|
ScopeThe CANopen application profile for extruder downstream devices include several parts: Part 1 specifies general definitions; Part 2 specifies the device profile for the puller downstream device; Part 3 specifies the device profile for the corrugator downstream device; Part 4 specifies the device profile for the saw downstream device; Part 5 specifies the device profile for the co-extruder device; Part 6 specifies the device profile for the calibration-table downstream device. NOTE All parts of this specification have been developed jointly with the European Committee of Machinery Manufacturers for the Plastics and Rubber Industries (Euromap) and is documented there as Euromap 27 . This part specifies the CANopen interface for the corrugator downstream device. |
2015-05-07 435 KB | PAS Login |
|
ScopeThe CANopen application profile for extruder downstream devices includes several parts: Part 1 specifies general definitions; Part 2 specifies the device profile for the puller downstream device; Part 3 specifies the device profile for the corrugator downstream device; Part 4 specifies the device profile for the saw downstream device; Part 5 specifies the device profile for the co-extruder device; Part 6 specifies the device profile for the calibration-table downstream device. NOTE All parts of this specification have been developed jointly with the European Committee of Machinery Manufacturers for the Plastics and Rubber Industries (Euromap) and is documented there as Euromap 27. This part specifies the CANopen interface for the saw downstream device. |
2015-05-07 438 KB | PAS Login |
|
ScopeThe CANopen application profile for extruder downstream devices includes several parts: Part 1 specifies general definitions Part 2 specifies the device profile for the puller downstream device Part 3 specifies the device profile for the corrugator downstream device Part 4 specifies the device profile for the saw downstream device Part 5 specifies the device profile for the co-extruder device Part 6 specifies the device profile for the calibration-table downstream device NOTE All parts of this specification have been developed jointly with the European Committee of Machinery Manufacturers for the Plastics and Rubber Industries (Euromap) and is documented there as Euromap 27. This part specifies the CANopen interface for simple and advanced co-extruder. |
2015-05-07 487 KB | PAS Login |
|
ScopeThe CANopen application profile for extruder downstream devices include several parts: Part 1 specifies general definitions Part 2 specifies the device profile for the puller downstream device Part 3 specifies the device profile for the corrugator downstream device Part 4 specifies the device profile for the saw downstream device Part 5 specifies the device profile for the co-extruder device Part 6 specifies the device profile for the calibration-table downstream device NOTE All parts of this specification have been developed jointly with the European Committee of Machinery Manufacturers for the Plastics and Rubber Industries (Euromap) and is documented there as Euromap 27. This part specifies the CANopen interface for calibration-tables. |
2015-05-07 556 KB | PAS Login |