
No. 4 - March 7, 2025
A word from the CiA Managing Director
The March issue of the CAN Newsletter magazine is online. It focuses on modular service robots. This includes also autonomous mobile robots (AMR) and automated guided vehicles (AGV). Though both are used for material transportation, there is a fundamental difference in their operation and flexibility:
- An AMR is a robot that operates autonomously and can navigate in an uncontrolled environment without the need for fixed paths or tracks.
- An AGV is a robot that follows fixed paths or tracks for material transportation, typically requiring infrastructure changes like magnetic tapes or wires.
Many AMRs and AGVs use embedded and deeply embedded CAN networks for both the navigation subsystem as well as the manipulation/handling subsystem. Unfortunately, the standardization of service robot modules is still in the beginning. One reason is the high number of variants. The production volume of service robot units is low compared with other consumer markets. But there are common modules, which could be standardized. The ISO/TC 299/WG 6 is developing a document series specifying the description of service robot module communication interfaces in XML (extended mark-up language). The first approach specified in ISO 22166-1 and ISO 22166-201 has some weaknesses. The description of communication interfaces is not detailed enough, in order to evaluate compatibility and interoperability of modules.
For example, the information about the used connector without the applied pin assignment for CAN-high and CAN-low is worthless. Additionally, the information of the used CAN data link layer version (CAN CC, CAN FD, or CAN XL) is missing. Just indicating CAN as used data link layer protocol is not sufficient. There is also no possibility to describe the CAN bit-rate options and the location of the sample point. This needs to be improved.
The standardized description of CAN-based interfaces for service robot modules is a nice idea, but what is really needed, are standardized profiles. This could include sensors for navigation units, for example, radar sensors. Other possible profiles could be those for wheel units and other actuators (e.g., for manipulation and handling purposes).
The market for modular service robots is not yet a high-volume one. But the nonprofit International Federation of Robotics (IFR) reported for 2023 a 30-percent increase for service robots, summing up to 205 000 units. Nearly 80 percent of the service robots are developed in Far East: China, Japan, and Korea are in the lead. Europe follows with 33 918 units. These figures seemed to be conservative, in my opinion. But there is no common and clear definition about what belongs to the service robot market. What is about agriculture robots used for harvesting purposes? What is about healthcare robots serving in hospitals?
“The service robotics industry is on the move: more and more robots are serving on factory floors, in shopping centers or helping with deliveries on the street,” said Marina Bill, the IFR president. In 2023, about half of the service robot market was installed for transportation and logistics.
The CAN community can help to reduce development effort, saving time and money. What is needed are volunteers to specify appropriate CAN-based profile specifications for service robot modules. If you are interested in such profiles and like to participate, you should contact me.
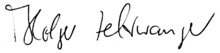
CiA Member Days 2025
The two-days event was participated by 40 individuals. There were two sessions with technical in-depth presentations. The presentation slides are available for CiA members on request from CiA office. Besides the CiA General Assembly, the CiA Member Days 2025 integrated also an open workshop titled “Ethernetification of CAN“ with contributions by Fraunhofer, Infineon, and JK Energy. The presentation slides are available on request for all interested parties.
CiA General Assembly 2025
The new CiA Board of Directors is the old one: Magnus-Maria Hell (CiA Technical Director), Christian Schlegel (CiA Business Director), and Holger Zeltwanger (CiA Managing Director) have been re-elected. The CiA General Assembly appointed Bosch, Emotas, esd electronics, Microcontrol, and Vector as CiA Business Committee members. The same companies have been elected as CiA Technical Committee members.
Pre-meeting: Profile for radar sensors
CiA office has scheduled an online meeting on March 20 (9:00, UTC+1) to discuss the idea of developing a device profile for radar sensors/scanners. In this meeting, CiA likes to discuss with CiA members the idea of a standardized profile to be mapped to CANopen and to J1939. This includes specifications for process data, configuration parameters, and diagnostic information.
This meeting addresses CAN-connectable radar sensor/scanner device suppliers as well as manufacturers of radar chips featuring CAN connectivity. Interested non-members may participate, as well. For more information, you may contact the CiA office.
ZVEI/CiA joint workshop "Welding and cutting"
ZVEI and CiA invite their members to participate in the joint workshop scheduled on April 8 (10:00 to 16:00, UTC+2) in Frankfurt am Main (Germany). During this workshop, the experts present the current status of standardization activities for the communication interfaces to connect devices within welding and cutting systems. This is an opportunity to contribute to the development of a unified solution for this industry. Especially device and system designers are asked to join the discussion and to share their expertise.
Registration for the workshop is obligatory and is possible following the link above.
Webinar: CAN FD status and future
In a one-hour webinar on March 20 (start 15:00, UTC+1), CiA introduces attendees into the CAN FD protocol. Presentation of CAN FD system design aspects and CAN FD in large-scale networks are on the agenda.
This webinar is free of charge, presentation language is English. Registration is obligatory and is possible via email.
CiA technology day: Benefits of CANopen FD
On April 03, CiA organizes an online technology day comprising several presentations in English language. The 3,5-hours event starts at 13:00 (UTC+2). Here, CiA engineers and experts from CiA member companies give an introduction into CANopen FD (CiA) and according device design (Emotas). Dynamic node and network addressing as well as electronic device description will be presented by CiA. Further, the experts give recommendations for CANopen FD system design (Microcontrol) and speak about integration of CANopen FD systems into the cloud (CiA). Cybersecurity in CANopen FD-based applications is also a topic presented by Embedded Systems Academy (EmSA).
The participation is free-of-charge. Registration is obligatory and is possible via email.
Meet CiA at Embedded World 2025
From March 11 to 13, CAN fellows have the opportunity to be informed about the latest CAN trends in a speech with CiA experts at the trade show. Meet CiA in the hall 1-203 to discuss any CAN-related topic. It is also possible to schedule an appointment in advance.
There are no “CAN messages”
CAN is a lower-layer communication technology, covering the OSI (open systems interconnection) data link and physical layers. There are three CAN data link layer protocols specified: CAN CC (classic), CAN FD (flexible data rate), and CAN XL (extended data-field length). These protocols specify different CAN data frame formats (CBFF, CEFF, FBFF, FEFF, and XLFF). There is no “CAN message” specified. The term “message” is an entity of the OSI application layer. There are “CANopen messages” (e.g., NMT, PDO, and SDO) and “J1939 messages “(e.g., PG and DM), for example.
By the way, the OSI transport layer uses the term “segment” and the OSI network layer exchanges “packets”. The ISO TP (transport protocol) specified in ISO 15765-2 uses the term “frame” instead of “segment”, which can cause confusion.
Keep terminology consistent: Never use the term “CAN message” in your data sheets and handbooks.
News ticker
+++ Hydrotechnik (Germany), a new CiA member offers the Multisystem 5700. Coming with two CAN interfaces supporting CANopen CC and J1939-21, it can measure pressure, temperature, and volume flow. +++ Copeland (U.S.A), another new CiA member is going to equip its refrigeration compressor with a CANopen interface; J1939 protocol stacks are already available. +++ CiA has assigned a CANopen vendor-ID to Macome (Japan), developing sensors for AGVs (automated guided vehicles). +++ Ematic (Italy) has a CANopen vendor-ID; the company provides hydraulic lift controllers. +++ The Micropower Group (Sweden) has received a CANopen vendor-ID; the company produces Li-ion batteries, chargers, and power supplies. +++
CiA activities
- CiA education and information events
- Charged online seminars
- Charged in-house seminars
- Free-of-charge CiA webinars
- CiA technolgy days
- CiA groups
- CiA trade shows
New CiA members since the last CCN
- Bever Car Products (NL)
- Hawe Hydraulik (DE)
- Jiangsu Fulling Motor Technology (JP)
- Micropower Group (SE)
- Optex (JP)
- Specialized Europe (CH)
CiA has 715 members (March 7, 2025)
Editors: Olga Fischer, Holger Zeltwanger (responsible according to the press law)
Advertising: Birgit Ruedel (responsible according to the press law)
CAN in Automation (CiA) e. V.
Kontumazgarten 3
90429 Nuremberg (Germany)
Tel. +49-911-928819-0
AG Nuremberg VR 200497
CAN Community News sign up
This 3-weekly free-of-charge email service provides CAN-related news to the entire CAN community. This includes reports about CiA activities, released CiA documents, available CiA publications, and other topics.
If you would like to subscribe to the CAN Community News please send an e-mail to mail(at)can-cia.org.